December 12, 2017
6 min read
Those Pesky Petrochemicals – Is There a Better Way?
SMost people don’t think too much about petrochemicals, but few of us could do without them. They are essential ingredients for many products we use every day.
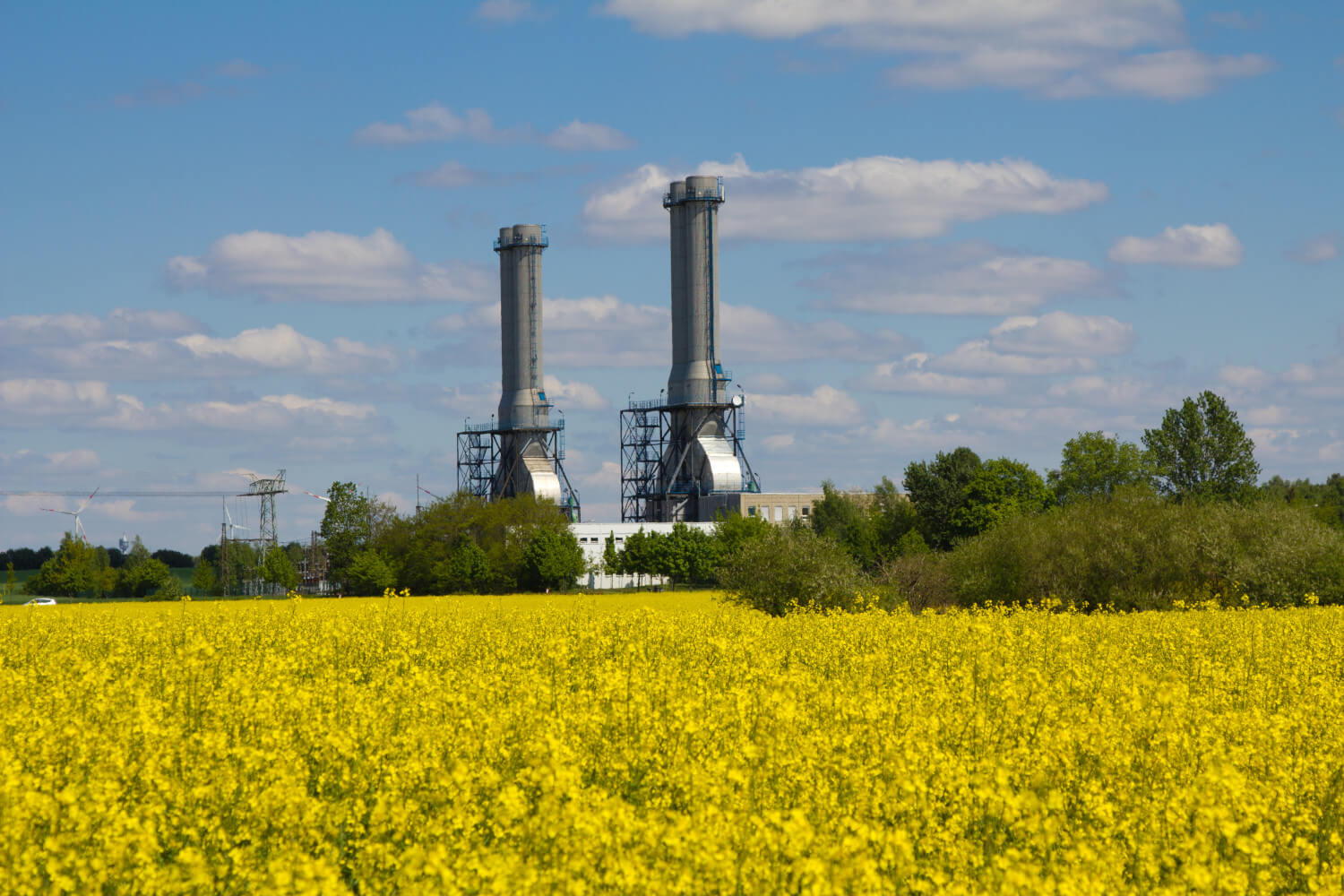
Where Do They Come From?
Most people don’t think too much about petrochemicals, but few of us could do without them. They are essential ingredients for many products we use every day. Petrochemicals are important components in carpet, baby bottles, TVs, detergents, smart phones, paint, computers, shoes and many other household items. Petrochemical compounds are necessary for many of the things we depend upon, but unfortunately the process to make them is costly, energy intensive and very harmful to the environment. We are fortunate however, that research is currently underway to develop alternative means of production to address these costs to society and the earth.
Most people don’t think too much about petrochemicals, but few of us could do without them. They are essential ingredients for many products we use every day. Petrochemicals are important components in carpet, baby bottles, TVs, detergents, smart phones, paint, computers, shoes and many other household items. Petrochemical compounds are necessary for many of the things we depend upon, but unfortunately the process to make them is costly, energy intensive and very harmful to the environment. We are fortunate however, that research is currently underway to develop alternative means of production to address these costs to society and the earth.
The biggest drawback of petrochemicals, of course, is that they are made primarily from oil (petrol). As the name suggests, oil is a fossil fuel formed millions of years ago, before the time of dinosaurs (hence, fossil). When used as a source of energy or converted into petrochemicals, fossil fuels release significant amounts of carbon into the atmosphere and surface water, resulting in increased greenhouse gases and global warming.
The petrochemical manufacturing process is particularly energy intensive and harmful to the environment. The complex mixture of hydrocarbons (compounds made of hydrogen and carbon) that comprises oil are separated into various fractions by distillation, a process that separates various compounds based on their boiling points.
“Light” fractions including propane and butane are separated from the crude oil at low temperatures (300 degrees C). Manufacturers then apply various chemical processes to generate a variety of petrochemicals. These chemicals are the starting points for the manufacture of plastics, the polyester used in carpet and clothing, and industrial solvents, oils and acids used in cleaning products. Many pharmaceuticals are also derived from petrochemicals, as are food additives, dyes, and explosives. Simply put, modern life would not be possible without petrochemicals.
The Downside of Petrochemicals
While we depend heavily on these materials, the process to make petrochemicals uses vast amounts of energy, and is toxic to the environment. In fact, the chemical and petrochemical industry is the heaviest industrial user of energy, accounting for more than 30% of total industry usage worldwide. Burning oil, natural gas and other fossil fuels, which releases harmful carbon dioxide (CO2) into the air, is the source for this energy. Making petrochemicals also requires a significant amount of oil as a raw material. Between 1971 and 2004, the demand for energy and raw materials for the chemical & petrochemical industry doubled.
While we depend heavily on these materials, the process to make petrochemicals uses vast amounts of energy, and is toxic to the environment. In fact, the chemical and petrochemical industry is the heaviest industrial user of energy, accounting for more than 30% of total industry usage worldwide. Burning oil, natural gas and other fossil fuels, which releases harmful carbon dioxide (CO2) into the air, is the source for this energy. Making petrochemicals also requires a significant amount of oil as a raw material. Between 1971 and 2004, the demand for energy and raw materials for the chemical & petrochemical industry doubled.
While the manufacture of petrochemicals consumes a large portion of the world’s energy, the biggest concern is the quantity of the harmful greenhouse gases generated in the process. Greenhouse gas emissions from the chemical sector in the US will increase by an estimated 45.8 million tons per year, as companies build or expand units that extract ethylene, propylene, methanol and other chemicals from natural gas liquids for use in manufacturing a wide variety of products. Obviously, cleaner alternatives for making petrochemicals are sorely needed.
Synthetic Biology and Synthetic DNA: A Viable Alternative for Production of Petrochemicals
Using synthetic biology methods to produce the carbon-based components for a variety of everyday products could reduce our dependency on burning fossil fuels. Several synthetic biology companies are now producing popular “green” alternatives. As noted in the recent Wired article “Cleaner Living Through Smarter Microbiology,” we will still use all the chemicals available today, but they will be made using synthetic DNA.
Synthetic biology applies research tools developed using molecular biology, biotechnology and other disciplines to redesign existing natural biological systems for useful purposes. These tools have already been used to engineer microbes and plants to make commercially valuable petrochemicals, several of which are already on the market. According to Dr. Craig Venter, a leading proponent of synthetic DNA, “The goal is to replace the entire petrochemical industry.” By using a renewable resource such as yeast or sugar, the end benefits would include less reliance on fossil fuel-based energy and reduced CO2 emissions.
There are many examples of successful production of the chemicals needed to make everyday items. Carpet made of a chemical produced by bacteria has been on the market for several years. A collaborative effort by DuPont and biotech company Genencor International (now part of DuPont) led to genetic modification of the bacteria to enable them to produce a chemical called PDO (1,3-propanediol) from corn sugar. Previously, PDO could only be produced from oil. PDO was in turn used to produce a unique fiber called Sorona®, which is now used by major carpet manufacturers including Mohawk and Karastan. Production of this “bio-fiber” required 43% less energy than nylon 6.6, one of the most commonly used fibers for production of premium carpet. Along with the energy savings, there is a corresponding 56 percent reduction in greenhouse gas emissions. DuPont claims the resulting carpet is “permanently stain-resistant… invitingly soft” and “incredibly durable.”
INVISTA, one of the world’s largest integrated producers of polymers and fibers, has entered into collaboration with Arzeda, a biotech company that “creates innovative cell factories that can transform or supplement current chemical production methods.” The initial goal is to produce biosynthetic butadiene (BD), a chemical needed to make synthetic rubber and various plastics. BD is also an important intermediate used by Invista to make ADN (adiponitrile), which is used in the manufacture of nylon 6.6.
The biotech company Genomatica has developed a process for the biological production of 1,4-BDO (1,4-butadienediol), a key ingredient in the production of polyurethanes and elastic fibers used in a wide range of products, from skateboards to Spandex. German chemical giant BASF has already put this process into production.
Genencor (DuPont) has created a biological process using modified bacteria to produce isoprene (synthetic rubber) with the trade name BioIsoprene™. Currently, Goodyear produced tires made from BioIsoprene™. This petrochemical replacement will “help reduce the tire and rubber industry’s dependence on oil-derived products.” As one of the world’s biggest users of isoprene to produce synthetic rubber, Goodyear’s commitment to biosynthesis of this chemical will help lessen the tire and rubber industry’s reliance on oil-derived products. Aside from tires, BioIsoprene™ can also be used in other products, including adhesives, golf balls and surgical gloves.
Acrylic acid is a key ingredient in many products, including adhesives, detergents, and diapers. OPX Biotechnologies teamed up with The Dow Chemical Company to modify bacteria to produce BioAcrylic acid with comparable performance and cost to the oil-based version, but with a 70% reduction in greenhouse gas emissions. OPX continues to innovate in developing biosynthetic products and has partnered with Evonik Industries AG to develop other specialty chemicals using the OPX processes.
Surfactants are widely used by industry and in consumer products, due to their properties as detergents, wetting agents, and emulsifiers. They are primarily organic acids, such as fatty-acyl-glutamate (FA-Glu). Modular Genetics recently developed an alternative bio-based process for production of FA-Glu utilizing genetically modified bacteria that are grown on soy bean hulls—which are an inedible byproduct of soy production. A whopping 70 billion pounds of inedible soy material are produced each year in the US alone. Using this synthetic biology process substantially reduces oil usage compared to conventional production methods.
The petrochemical industry consumes large quantities of energy and generates vast amounts of greenhouse gases and other dangerous air pollutants. However, society is absolutely dependent on the resulting chemicals to provide all the products required for our modern lifestyle. Synthetic biology approaches are already providing a much more sustainable means for producing these chemicals, with the potential to make a very significant impact on our environment by eventually replacing most petrochemical products.
What did you think?
Like
Dislike
Love
Surprised
Interesting
Read Next
Get the latest by subscribing to our blog